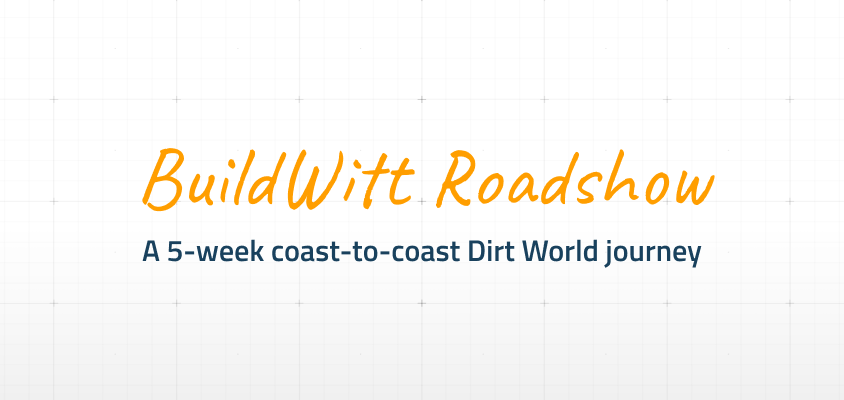
Day 23 - Big Rocks into Small Rocks
Day 23 technically started on the afternoon of day 22 since we wrapped up with ASN Constructors in Fargo around lunch.
Next was visiting my friend John Scepaniak with WD Scepaniak, a company specializing in mobile crushing spreads.
Your life wouldn’t be much without crushed rock. As a key ingredient in concrete, asphalt, and any building pad, crushed rock is the foundation of society. No one wants to be the fool who builds their house upon sand…
Crushed rock usually comes from quarries, which blast and crush vast quantities of rock using permanent crushers, screens, and conveyors.
BUT… What if you need crushing services only a few weeks or months out of the year? That’s when you call WD Scepaniak.
Thanks to their many different mobile crushing spreads, they can drive their equipment anywhere via semi-truck, set it up in only days, and CRUSH. When finished, they pack everything up and go to the next one.
Their first project we visited was across the ND / MN border amongst... More cornfields! As I barreled down the dirt roads in the RV, I noticed two enormous piles of processed aggregate in the distance—our destination.
WD Scepaniak was creating base material for a customer from a sand and gravel deposit amongst the farmland. Starting with a 988 loader, they dug the material from the face one bucket at a time without blasting required. The loader then carried the material roughly 100 yards to a feeder, which started the processing.
The “issue” with the native material was the high fines content. But thanks to the flexibility of their plants, it was no drama. As the material fed into the plant via a conveyor, it hit a splitter, dividing the material flow in two. The first flow went to a screen deck which removed all fines and directed the sandy material to a waste pile. The leftover rock cycled to the second half of the plant, which created the final product.
As a second screen deck separated the fines from the rock, anything big enough went into a cone crusher, reducing the rock to 2” or less. After sizing, the stone mixed with the reduced fines and ended up on a stacker for stockpiling.
In only an hour, we watched the crew make thousands of tons of Minnesota-spec base material from what was untouched earth.
NEAT
The second spread we checked out was more unique—we arrived at the security shack for a fine stone manufacturing facility. The products? Countertops and gravestones.
They waved us through, and we weaved through beautiful chunks of raw stone, awaiting their turn for cutting and finishing within the enormous facility. But that’s not what we were there to see… In the back of the yard was a massive pile of scrap granite and marble, where WD Scepaniak was… you guessed it… crushing it!
Once a year, they mobilize a crushing spread to process the waste material from the plant into valuable crushed granite for landscaping and base material. Using two 980 loaders, they fed the chunks into the plant, which crushed everything with a jaw and cone crusher. After hitting the screen deck, multiple products emerged at the other end in neat piles, ready to sell to the local market.
DOUBLE NEAT
Between my visits with Scepaniak, I’d also like to give honorable mention to T Scherber, Minger, Blattner, and Veit. I tried to make the most of my time in the Twin Cities area by seeing as many folks as possible!
And that was Minnesota… Onwards to our country’s cheese curd capital!